High nickel & Chromium Alloys
High nickel & Chromium biased Alloys are one of the products that we keep in stock and can be supplied at very short notice with Original Manufacturers Material Test certificate.
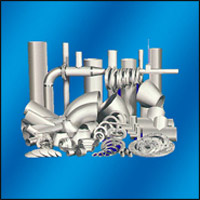
DESCRIPTION
Alloy 20 is one of the so-called "Super" stainless steels that was designed for maximum resistance to acid attack. Its nickel, chromium, molybdenum and copper content contribute to its overall resistance to to chloride on stress corrosion cracking and general pitting attack. The alloy is stabilized with columbium to minimize carbide precipitation during welding. It has good mechanical properties and can be fabricated with comparative ease. Although the alloy was designed for use in sulfuric acid related industries, it finds wide usage throughout the chemical processing industry. It also is used for processing pharmaceuticals, food, gasoline, solvents, plastics, explosives, synthetic fibers and many other products.
DESIGN FEATURES• Superior resistance to stress-corrosion
cracking in boiling 20 to 40% sulfuric acid.
• Excellent general corrosion resistance to
sulfuric acid.
• Excellent resistance to chloride stress
corrosion cracking.
• Excellent mechanical properties and
fabricability.
• Minimal carbide precipitation during welding.
TYPICAL APPLICATIONS
Chemical and allied industries
Food and dye production
Heat exchangers
SO 2 scrubbers and other severe environments
Tanks
Pickling racks
Valves
TENSILE REQUIREMENTS
Tensile Strength (KSI) 80
Yield Strength (KSI) 35KSI can be converted to MPA (Megapascals) by multiplying by 6.895.
AVAILABILITY
Seamless Pipe 1/2" - 8"
Weld Pipe 1/2" - 12"
Butt-Weld Fittings 1/2" - 12"
Flanges 1/2" - 12"
Pressure Fittings 1/2" - 2"
150# Fittings 1/4" - 2"
Tubing 1/4", 3/8", 1/2"
Valves 1/2" - 12"
Bar 1" - 8"
SPECIFICATIONS
ASTM B729, B464, B366, B473, B462
ASME SB729, SB464, SB366, SB473, SB462
DESCRIPTION
Avesta Sheffield 2205 is a ferritic-austenitic stainless steel which combines many of the beneficial properties of both ferritic and austenitic steels. As a result of high chromium and molybdenum contents, the steel has very good pitting and uniform corrosion resistance to stress corrosion cracking as well as high mechanical strength.
2205 has good weldability and can be welded using most of the welding techniques for stainless steels. Due to the balanced composition, when welded correctly, the heat affected zone contains sufficient austenite to avoid the risk of localized corrosion. The chemical composition of 2205 is balanced to give a microstructure containing roughly equal amounts of ferrite and austenite.
DESIGN FEATURES
• High strength.
• Low thermal expansion and higher heat
conductivity than austenitic steels.
• High resistance to stress corrosion cracking,
corrosion fatigue and erosion.
• High uniform corrosion resistance.
• High pitting and crevice corrosion
resistance.
• Good sulfide stress corrosion cracking
resistance.
TYPICAL APPLICATIONS
• Heat exchangers, tubes and pipe for production and handling of gas and oil
• Heat exchangers and pipes in desalination plants
• Pressure vessels, pipes, tanks and heat exchangers for processing and transport of various chemicals
• Pressure vessels, tanks and pipes in process industries handling chlorides
• Rotors, fans, shafts and press rolls where the high corrosion fatigue strength can be utilized
• Cargo tanks, piping and welding consumables for chemical tankers
TENSILE REQUIREMENTS
Tensile Strength (KSI) 65
Yield Strength (KSI) 90KSI can be converted to MPA (Megapascals) by multiplying by 6.895.
AVAILABILITY
Seamless Pipe 1/2" - 8"
Weld Pipe 1/2" - 12"
Butt-Weld Fittings 1/2" - 12"
Flanges 1/2" - 8"
Bar 1" - 8"
SPECIFICATIONS
ASTM A790, A815, A182
ASME SA790, SA815, SA182
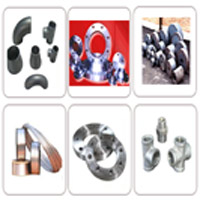
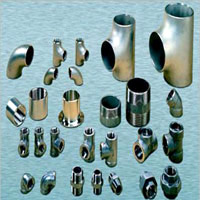
AVAILABILITY
Weld Pipe 1/2" - 12"
Butt-Weld Fittings 1/2" - 12"
Flanges 1/2" - 12"
Valves 1/2 - 8"
Bar 1" - 9"
SPECIFICATIONS
ASTM B619, B366, B564, B574
ASME SB619, SB366, SB564, SB574
DESCRIPTION
Alloy C-276 is an improved wrought version of Alloy C and has the same excellent corrosion resistance as that material but has greatly improved fabricability. It can be hot worked and cold formed by conventional procedures. It can be joined by all of the common welding methods and resists the formation of grain boundary precipitates in the weld-affected zone, thus making it suitable for most chemical process applications in the aswelded condition. It resists pitting and stress-corrosion cracking and is resistant to oxidation at temperatures up to 1900 deg.F.
DESIGN FEATURES
• Outstanding corrosion resistance and oxidizing environments.
• Excellent resistance to pitting and stress-corrosion cracking.
• Maintains corrosion resistance in welded joints.
TYPICAL APPLICATIONS
Chemical processing Pollution control Pulp and paper Other severe environments and/or conditions.
TENSILE REQUIREMENTS
Tensile Strength (KSI) 100
Yield Strength (KSI) 41KSI can be converted to MPA (Megapascals) by multiplying by 6.895.
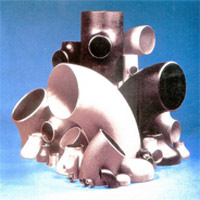
AVAILABILITY
Seamless Pipe 1/2" - 8"
Weld Pipe 8" - 12"
Butt-Weld Fittings 1/2" - 8"
Bar 1" - 8"SPECIFICATIONS
ASTM A312, A403, A182
ASME SA312, SA403, SA182
DESCRIPTION
310S has excellent resistance to oxidation under constant temperatures to 2000 deg. F. Cyclic conditions reduce its oxidation resistance, and a maximum operating temperature of 1900 deg.F. is generally recommended if cycling is involved. Having a lower coefficient of expansion than most 300 stainless steels, 31OS may be used in operations involving moderately severe thermal cycling, such as rapid air cooling. It is not usually recommended for liquid quenching. Although 310S has less resistance to absorption of carbon and nitrogen than the higher alloys such as 330 and 333, it is widely used in moderately carburizing atmospheres such as encountered in petro-chem plants. Because of its high chromium and medium nickel contents, 310S may be used in atmospheres containing moderate amounts of sulfur.
DESIGN FEATURES
• Austenitic stainless steel with excellent high
temperature oxidation resistance.
• Good for continuous exposure to 2100 deg.F. intermittent service to 1900 deg.F.
• Better elevated temperature creep strength than the 18-8 grades.
• Good resistance to both carburizing and reducing environments.
• General corrosion resistance better than Types 304 and 309.
• May be susceptible to chloride stress corrosion cracking.
• Availability.
• Ease of fabrication.
TYPICAL APPLICATIONS
Heat exchanger and heat recuperator tubing
Molten salt applications
Sulfur bearing gas atmospheres
TENSILE REQUIREMENTS
Tensile Strength (KSI) 75
Yield Strength (KSI) 30
KSI can be converted to MPA (Megapascals) by multiplying by 6.895
DESCRIPTION
Avesta Sheffield 2205 is a ferritic-austenitic stainless steel which combines many of the beneficial properties of both ferritic and austenitic steels. As a result of high chromium and molybdenum contents, the steel has very good pitting and uniform corrosion resistance to stress corrosion cracking as well as high mechanical strength.
2205 has good weldability and can be welded using most of the welding techniques for stainless steels. Due to the balanced composition, when welded correctly, the heat affected zone contains sufficient austenite to avoid the risk of localized corrosion. The chemical composition of 2205 is balanced to give a microstructure containing roughly equal amounts of ferrite and austenite.DESIGN FEATURES
• High strength.
• Low thermal expansion and higher heat
conductivity than austenitic steels.
• High resistance to stress corrosion cracking,
corrosion fatigue and erosion.
• High uniform corrosion resistance.
• High pitting and crevice corrosion
resistance.
• Good sulfide stress corrosion cracking
resistance.
TYPICAL APPLICATIONS
• Heat exchangers, tubes and pipe for production and handling of gas and oil
• Heat exchangers and pipes in desalination plants
• Pressure vessels, pipes, tanks and heat exchangers for processing and transport of various chemicals
• Pressure vessels, tanks and pipes in process industries handling chlorides
• Rotors, fans, shafts and press rolls where the high corrosion fatigue strength can be utilized
• Cargo tanks, piping and welding consumables for chemical tankers
TENSILE REQUIREMENTS
Tensile Strength (KSI) 65
Yield Strength (KSI) 90KSI can be converted to MPA (Megapascals) by multiplying by 6.895.
AVAILABILITY
Seamless Pipe 1/2" - 8"
Weld Pipe 1/2" - 12"
Butt-Weld Fittings 1/2" - 12"
Flanges 1/2" - 8"
Bar 1" - 8"
SPECIFICATIONS
ASTM A790, A815, A182
ASME SA790, SA815, SA182
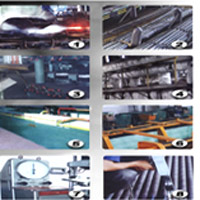
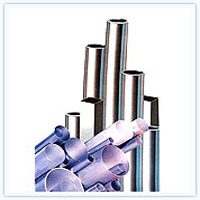
AVAILABILITY
Seamless Pipe 1/2" - 12"
Weld Pipe 8" - 12"
Butt-Weld Flanges 1/2" - W
Bar 1" - 12"
SPECIFICATIONS
ASTM A312, A403, A182, A479, A276
ASME SA312, SA403, SA182, SA479, SA276
DESCRIPTION
These types of stainless are austenitic chromium steels containing columbium. They are recommended for parts fabricated by welding which cannot be subsequently annealed. These types also are used for parts which are intermittently heated and cooled to temperatures between 800 deg. and 1600 deg.F. The addition of columbium produces a stabilized type of stainless that eliminates carbide precipitation, and consequently, intergranular corrosion.
DESIGN FEATURES
• Superior general corrosion resistance over Type 321 due to stabilization with columbium.
• Reduced tendencies to form continuous networks of chromium carbides at the grain boundaries.
• Better high temperature properties than 304 or 304L. Generally used for parts which are intermittently heated up to 1500 deg. F. For continuous service the maximum temperature is 1650 deg. F.
• Type 347H has high carbon (.04 - . 10) for better high temperature creep properties.
• Improved intergranular corrosion resistance.
TYPICAL APPLICATIONS
High temperature chemical process, heat exchanger tubes
Refineries
High temperature steam service
TENSILE REQUIREMENTS
Tensile Strength (KSI) 75
Yield Strength (KSI) 30
KSI can be converted to MPA (Megapascals) by multiplying by 6.89
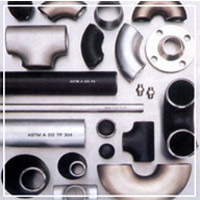
GENERAL PROPERTIES
The AL-6XN alloy is a superaustenitic stainless steel which was developed by Allegheny Ludlum Corporation. It exhibits far greater resistance to chloride pitting, crevice corrosion and stress-corrosion cracking than exhibited by the standard 300 series stainless steels, and is less costly than the traditional nickel-base corrosion resistant alloys.
The AL-6XN alloy has exhibited good performance in variety of highly corrosive environments. The AL-6XN alloy is available in a wide range of product forms including plate, strip, sheet, bar, billet, tubing, pipe, and castings. Its various product forms are covered by ASME and ASTM specifications. The use of wrought AL-6XN products in the ASME Boiler and Pressure Vessel is covered by Code Case 1997 (latest revision) for Section VIII construction and by Code Case N-438 (latest revision) for Section III construction. The use of AL-6XN castings is covered by Code Case 2106 (latest revision) for Section VIII and Code Case 497 (latest revision) for Section III construction. The alloy is approved for both welded and unwelded construction under ANSI/ASME B31.1 Code Case 155. Use of AL-6XN alloy in contact with hydrogen sulfide-containing petroleum and natural gas is covered by NACE MR0175-92.
AVAILABILITY
Weld Pipe 3/4"- 12"
Butt-Weld Fittings 3/4" - 12"
Flanges 3/4" - 12"
Bar 1" - 8"
SPECIFICATIONS
ASTM A312, A403, A182
ASME SA312, SA403, SA182
DESCRIPTION
254SMO is an austenitic stainless steel designed for maximum resistance to pitting and crevice corrosion. With high levels of chromium, molybdenum, and nitrogen, 254SMO is especially suited for high chloride environments such as brackish water seawater pulp mill bleach plants and other high chloride process streams. 254SMO offers chloride resistance superior to that of Alloy 904L Alloy 20, Alloy 825 and Alloy G. 254SMO is compatible with the common austenitic stainless steels. It is often used as a replacement in critical components of larger constructions where Type 316L or 317L has failed by pitting, crevice attack, or chloride stress corrosion cracking. In new construction, 254SMO has been found in many cases to be a technically adequate and much less costly substitute for nickelbased alloys and titanium. 254SMO is substantially stronger than the common austenitic grades, but is also characterized by high ductility and impact strength. 254SMO is readily fabricated and welded.
(R) 254SMO is A REGISTERED TRADEMARK OF AVESTA SHEFFIELD
DESIGN FEATURES
High resistance to pitting, crevice and general corrosion.
Very high resistance to chloride stress corrosion cracking.
50% stronger than 300-series austenitic stainless steels.
Excellent impact toughness.
Excellent workability and weldability.
TYPICAL APPLICATIONS
Seawater handling equipment
Pulp mill bleach systems
Tall oil distillation columns and equipment
Chemical processing equipment
Food processing equipment
Desalination equipment
Flue gas desulfurization scrubbers
Oil and gas production equipment
TENSILE REQUIREMENTS
Tensile Strength (KSI) 94
Yield Strength (KSI) 44
KSI can be converted to MPA (Megapascals) by multiplying by 6.895.
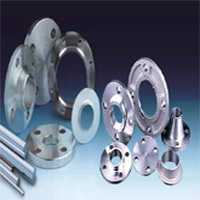
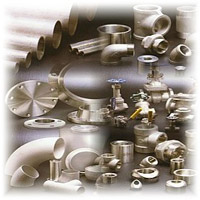
AVAILABILITY
Seamless Pipe 1/2" - 12"
Butt-Weld Fittings 1/2" - 12"
Flanges 1/2" - 12"
SPECIFICATIONS
ASTM B221, B361, B247
DESCRIPTION
Aluminum has been proven to be the economical choice for a wide variety of applications. Its cost effectiveness and lightweight characteristics make it a popular grade of material in petroleum and petrochemical industries. Aluminum also serves the food, beverage and drug industries. A cubic inch of Aluminum weighs about one-tenth of a pound. Its color is like that of silver. The "commercially" pure metal has a faintly bluish tinge. Its atomic weight is 26.98 pure. Aluminum melts at a temperature of 1220 deg.F. (or 660 deg.C). The ability of aluminum to transmit heat rapidly and efficiently makes it an ideal material for heat transfer processes, cryogenic applications and similar uses. Its resistance to corrosion often results in longer service life and reduced maintenance.
• One third the weight of most metals.
• Exceptional corrosion properties.
• Non-toxic; Maintains the color and purity of many products.
• Non-magnetic.
• Good conductivity and reflectability.
• Good workability and machinability.
TYPICAL APPLICATIONS
General fluid transmission and process piping
Portable and temporary piping
Hydraulic pressure fines
Heat transfer and cryogenic processes
Structural
Ornamental and architectural
TENSILE REQUIREMENTS
Tensile Strength 38,000 PSI
Yield Strength 35,000 PSI
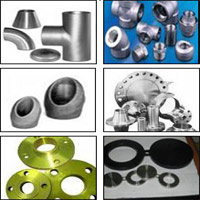
AVAILABILITY
Weld Pipe 1/2" - 12"
Seamless Pipe 1/2" - 8"
Butt-Weld Fittings 1/2" - 12"
Flanges 1/2" - 12"
Bar 1"- 8"
SPECIFICATIONS
ASTM A312, A403, A182
ASME SA312, SA403, SA182
DESCRIPTION
317L is a molybdenum bearing austenitic chromium nickel steel similar to type 316 except the alloy content in 317L is somewhat higher. It has superior corrosion resistance in special applications where it is desired to reduce contamination to a minimum. 317L was developed primarily to resist more effectively the attack of sulfurous acid compounds. However, its proven ability to combat corrosion has widened its use considerably and is now being used for many other industrial applications. The low carbon content of 317L provides immunity to intergranular corrosion in applications where heavy cross-sections cannot be annealed after welding or where low temperature stress relieving treatments are desired.
DESIGN FEATURES• A molybdenum bearing austenitic chromium nickel steel with an alloy content somewhat higher than the 316 grades.
• Superior corrosion resistance in difficult
environments.
• Higher creep, stress-to-rupture and tensile
strengths than other stainless steels.
• Reduced intergranular precipitation of chromium carbides during welding and stress relieving as well as minimized possibility of corrosion failure from intergranular attack due to low carbon content.
• Resistance to pitting and crevice corrosion making 317L a successful life-cost product in a variety of highly corrosive environments.
TYPICAL APPLICATIONS
Flue gas desulfurization scrubber systems
Chemical and petro-chemical processing equipment
Pulp and paper plants
Food processing equipment
Textile equipment
TENSILE REQUIREMENTS
Tensile Strength (KSI) 75
Yield Strength (KSI) 30
KSI can be converted to MPA (Megapascals) by multiplying by 6.895.
AVAILABILITY
Seamless Pipe 1/2" W
SPECIFICATIONS
ASTM B677, B366
ASME SB677, SB366
DESCRIPTION
904L is a high-alloy austenitic stainless steel with low carbon content. The grade is intended for use under severe corrosive conditions. It has been application proved over many years and was originally developed to resist corrosion in dilute sulfuric acid. It is standardized and approved for pressure vessel use in several countries. Structurally, 904L is fully austenitic and is less sensitive to precipitation ferrite and sigma phases than conventional austenitic grades with high molybdenum content. Characteristically, due to the combination of relatively high contents of chromium, nickel, molybdenum and copper 904L has good resistance to general corrosion, particularly in sulfuric and phosphoric conditions.
Good resistance to pitting and crevice corrosion.
Very good resistance to stress corrosion cracking.
Good resistance to intergranular corrosion.
Good formability and weldability.
Maximum service temperatures of
450 deg.C. (824 deg.F).
TYPICAL APPLICATIONS
Production and transport of sulfuric acid
Metal pickling in sulfuric acid
Production and concentration of phosphoric acid
Use in seawater, brackish water, condensers, heat exchangers and pipe work in general
Paper and allied industries
Gas washing
Chemical and pharmaceutical industries
TENSILE REQUIREMENTS
Tensile Strength (KSI) 70
Yield Strength (KSI) 25
KSI can be converted to MPA (Megapascals) by multiplying by 6.895.
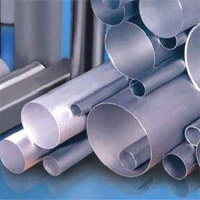
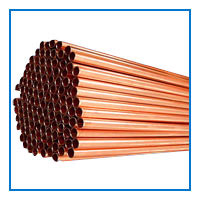
AVAILABILITY
Seamless Pipe 1/2" - 8"
SPECIFICATIONS
ASTM A268, A815, A182
DESCRIPTION
Type 410 is a martensitic stainless steel which is magnetic, resists corrosion in mild environments and has fairly good ductility. 410 pipe is used where abrasion and wear resistance is needed, combined with fair resistance to general corrosion and oxidation.
DESIGN FEATURES
Martensitic stainless steel with high mechanical properties.
Ferromagnetic in the annealed or hardened condition.
Contains minimum amount of chromium to impart stainless steel properties.
Resists oxidation and scaling up to 1200 deg.F.
Resists abrasion and wear better than most 300 series stainless steels.
Good sulphide stress corrosion cracking resistance
Hardness in one 410's best features
TYPICAL APPLICATIONS
Pipelines transporting fluids mixed with solids like coal, sand or gravel
TENSILE REQUIREMENTS
Tensile Strength (KSI) 60
Yield Strength (KSI) 30
KSI can be converted to MPA (Megapascals) by multiplying by 6.895.
AVAILABILITY
Seamless Pipe 1/4" - 20"
Weld Pipe 1/2" - 24"
Butt-Weld Fit. 1/2" - 24"
Butt-Weld Fit. 1/2" - 12"
Pressure Fittings 1/4" - 4"
150# Fittings/Nipples 1/4" - 4"
Valves 1/2" - 24"
Tubings 1/4", 3/8", 1/2", 3/4", 1"
Flanges 1/2" - 24"
Bar 1/8" - 12"
SPECIFICATIONS
ASTM A312, A376, A358, A269, A249, A403, A182, A351
ASME SA312, 5A376, SA358, SA269, SA249, SA403, SA182, SA351
DESCRIPTION
304 stainless is a low carbon (0.08% max) version of basic 18-8 also known as 302. Type 302 has 18% chromium and 8% nickel. Type 304 has slightly lower strength than 302 due to its lower carbon content. Type 304 finds extensive use in welding applications because the low carbon permits some exposure in the
carbide precipitation range of 800 0 F - 1500 OF without the need for post-annealing operations. However, the severity of corrosive environments may necessitate annealing after welding or the use of 304L. Type 304L has a carbon content of 0.03% or less. This alloy can be used in the as-welded condition without becoming susceptible to intergranular corrosion.
Oxidation resistance up to 1650 0 F for
continuous service and up to 1 1500 deg.F where cyclic heating is involved.
General purpose corrosion resistance.
Non-hardenable except by cold working.
Non-magnetic except when cold worked.
May be susceptible to chloride stress corrosion cracking.
Used where field working is employed.
TYPICAL APPLICATIONS
Sanitary
Dairy and Food processing
Heat exchangers, evaporators
Feedwater heaters
TENSILE REQUIREMENTS
Tensile Strength (KSI) 70
Yield Strength (KSI) 25
KSI can be converted to MPA (Megapascals) by multiplying by 6.895.
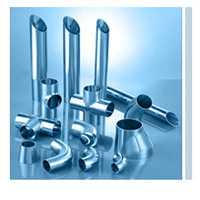
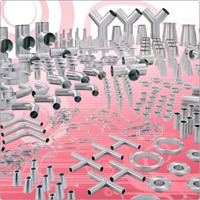
AVAILABILITY
Seamless Pipe 1 /4" - 20"
Weld Pipe 1/2" - 24"
Butt-Weld Fittings 1/2" - 24"
Butt-Weld Fittings 1/2" - 12"
Flanges 1/2" - 24"
Pressure Fittings 1/4" - 4"
150# Fittings/Nipples 1/4" - 4"
Valves 1/2" - 24"
Tubings 1/4", 3/8", 1/2 3/4", 1"
Bar 1/8" - 12"
SPECIFICATlONS
ASTM A312, A376, A358, A269 A249, A403, A182, A351 A479, A276
ASME SA312, SA376, SA358, SA269, SA249, SA182, SA276, SA403, SA479, SA351
DESCRIPTION
Type 316 is a molybdenum steel possessing improved resistance to pitting by solutions containing chlorides and other halides. In addition, it provides excellent elevated temperature tensile, creep and stress - rupture strengths.
DESIGN FEATURES
• Type 316 is more resistant to atmospheric and other mild environments than Type 304. It is resistant to dilute solutions (i.e. 1-5%) of sulfuric acid up to 120 deg.F. However, in certain oxidizing acids, Type 316 is less resistant than Type 304.
• 316 is susceptible to carbide precipitation when exposed in the temperature range of 800 deg. - 1500 deg.F. and therefore is susceptible to intergranular corrosion in the as-welded condition.
• Annealing after welding will restore corrosion resistance.
• Type 316L has the same composition as Type 316 except the carbon content is held below 0.03%. Not unexpectedly, its general corrosion resistance and other properties closely correspond to those of Type 316. However, it does provide immunity to intergranular attack in the as-welded condition or with short periods of exposure in the temperature range of 800 deg. - 1500 deg.F. The use of 316L is recommended when exposure in the carbide precipitation range is unavoidable and where annealing after welding is not practical. However, prolonged exposure in this range may embrittle the material and make it susceptible to intergranular attack.
• The maximum temperature for scaling resistance in continuous service is about 1650 deg. F. and 1500 deg.F. for intermittent service.
• May be susceptible to chloride stress corrosion cracking.
• Non-hardenable; non-magnetic in the annealed condition, and slightly magnetic when cold worked.
• Improved corrosion resistance to chlorides.
TYPICAL APPLICATIONS
Nuclear, chemical processing, Rubber, plastics, pulp/paper, pharmaceutical and textile industries, heat exchangers, condensers and evaporators
TENSILE REQUIREMENTS
Tensile Strength (KSI) 70
Yield Strength (KSI) 25
KSI can be converted to MPA (Megapascals) by multiplying by 6.895.
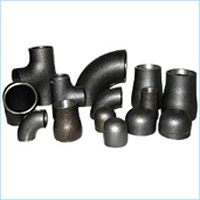
AVAILABILITY
Seamless Pipe 1/2" - 8"
Weld Pipe 8" - 12"
Butt-Weld Fittings 1/2" - 8"
Bar 1" - 6"
Flanges 1/2" - 8"
Pressure Fittings 1/2" - 2"
SPECIFICATIONS
ASTM B161, B162, B366, B160, B564
ASME SB161, SB162, SB366, SB160, SB564
DESCRIPTION
Alloy 200 is an unalloyed wrought nickel. It offers excellent corrosion resistance, good mechanical, magnetic and magnetostrictive properties and useful thermal and electrical conductivities.
DESIGN FEATURES
• Excellent resistance to many corrosive media from acid to alkaline.
• Extremely high resistance to caustic alkalis including the molten state.
• Resistance to mineral acids varies according to temperature and concentration and whether or not the solution is aerated. Corrosion resistance is better in non-aerated acids.
• In acid, alkaline and neutral salt solutions, Alloy 200 shows good resistance, however, severe attack occurs in oxidizing salt solutions.
• Resistant to all dry gases at room temperature.
TYPICAL APPLICATIONS
Food production, such as the handling of cool brines, fatty acids and fruit juices
Vessels in which fluorine is generated and reacted with hydrocarbons
Storing and transportation of phenol-immunity from any form of attack ensures absolute product purity
Manufacture and handling of sodium hydroxide, particularly at temperatures above 570 deg.F
Production of viscose rayon and manufacture of soap - general corrosion resistance and virtual immunity to intergranular attack above 600 deg.F
Production of hydrochloride and chlorination of hydrocarbons such as benzene, methane and ethane
TENSILE REQUIREMENTS
Tensile Strength (KSI) 58
Yield Strength (KSI) 18
KSI can be converted to MPA (Megapascals) by multiplying by 6.895.
AVAILABILITY
Seamless Pipe 1/2" - 8"
Weld Pipe 8" - 12"
Butt-Weld Fittings 1/2" - 8"
Flanges 1/2" - 8"
Bar 1" - 8"
Pressure Fittings 1/2" - 2"
150# Fittings 1/4" - 1"
Tubing 1/4", 3/8", 1/2"
Valves 1/2" - 12"
SPECIFICATIONS
ASTM B165, B127, B366, B164, B564
ASME SB165, SB127, SB366, SB164,S8564
DESCRIPTION
Alloy 400 is used for its excellent combination of corrosion resistance, strength, ductility and weldability The corrosion resistance in seawater is especially good under high velocity conditions. Alloy 400 also is generally not susceptible to stress corrosion cracking.
DESIGN FEATURES
• Outstanding resistance to neutral and alkaline salt.
• One of few metallic materials which can be used in contact with fluorine, hydrofluoric acid, hydrogen fluoride and their derivatives.
• High resistance to caustic alkalis.
• Can be used in contact with dilute solutions of mineral acids such as sulfuric and hydrochloric, particularly if they are nonaerated.
• Resistance to chloride induced stress corrosion cracking.
• Good mechanical properties from sub-zero temperatures up to 1020 deg.F.
TYPICAL APPLICATIONS
Feed-water and steam generator tubing in power plants
Brine heaters and evaporator bodies in salt plant
Sulfuric and hydrofluoric acid alkylation plant
Industrial heat exchangers
Cladding for crude oil distillation columns
Splash-zone sheathing in offshore structures
Propeller and pump shafts for seawater service
Plant for uranium refining and isotope separation in the production of nuclear fuel
Pumps and valves used in the manufacture of chlorinated hydrocarbons
Monoethanolamine (MEA) reboiler tubes
TENSILE REQUIREMENTS
Tensile Strength (KSI) 81
Yield Strength (KSI) 36
KSI can be converted to MPA (Megapascals) by multiplying by 6.895.
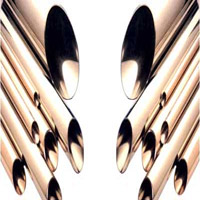

AVAILABILITY
Seamless Pipe 1/2" - 8"
Butt-Weld Fittings 1/2" - 8"
Flanges 1/2" - 8"
Bar 1" - 8"
SPECIFICATIONS
ASTM B167, B366, 8166, 8564
ASME SB167, SB366, SB166, SB564
DESCRIPTION
Alloy 600 is a nickel chromium iron alloy used for applications which require resistance to corrosion and heat. The alloy also has excellent mechanical properties and presents the desirable combination of high strength and good workability under a wide range of temperatures.
DESIGN FEATURES
High nickel content offers excellent resistance to corrosion by many organic and inorganic compounds.
Virtually immune to chlorideon stress corrosion cracking.
Chromium confers resistance to sulfur compounds and provides resistance to oxidizing conditions at high temperatures or in corrosive solutions.
Alloy 600 is not precipitative hardenable, it is hardened and strengthened only by cold work.
Good for a variety of applications involving temperatures from cryogenic to above 20000 F
TYPICAL APPLICATIONS
Steam generators
Chemical processing
Food processing
Superheaters
Jet engines
Electronic parts
TENSILE REQUIREMENTS
Tensile Strength (KSI) 80
Yield Strength (KSI) 35
KSI can be converted to MPA (Megapascals) by multiplying by 6.895.
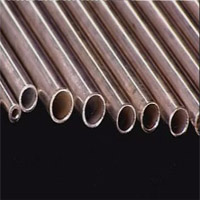
AVAILABILITY
Welded Pipe 1/2" - 8"
Butt Weld Fittings 1/2" - 8"
Flanges 1/2" - 8"
Bar 1" - 4-1/2"
SPECIFICATION
ASTM 8443, 8705, B366, B446, B564
ASME SB443, SB705, SB366, SB446, SB564
DESCRIPTION
Alloy 625 is a nickel-Chromium alloy used for its high strength, excellent fabricability and outstanding corrosion resistance. Service temperatures range from cryogenic to 1800 deg.F. Alloy 625 strength is derived from the stiffening effect of molybdenum and columbium on its nickel-Chromium matrix; thus precipitation-hardening treatments are not required. This combination of elements also is responsible for superior resistance to a wide range of corrosive environments of unusual severity as well as to high-temperature effects such as oxidation and carburization.
DESIGN FEATURES
Outstanding resistance to pitting, crevice corrosion, impingement corrosion and intergranular attack.
Almost complete freedom from Chloride induced stress corrosion cracking.
Good resistance to mineral acids, such as nitric, phosphoric, sulphuric and hydrochloric acids.
Good resistance to alkalis and organic acids.
Good mechanical properties.
TYPICAL APPLICATIONS
Used for structures in contact with seawater and Subject to high mechanical stresses
Flue gas scrubbers components
Chimney linings
Superphosphoric acid production equipment
Sour gas production tubes
Offshore industry, marine equipment
High tensile, creep, rupture strength, outstanding fatigue and thermal-fatigue strength; oxidation resistance; and excellent weldability and brazeability make it a good choice in the aerospace industry
TENSILE REQUIREMENTS
Tensile Strength (KSI) 120
Yield Strength (KSI) 60
KSI can be converted to MPA (megapascals) by multiplying by 6.895.
AVAILABILITY
Seamless Pipe 1/2" - 8"
Welded Pipe 8" - 12"
Butt-Weld Fittings 1/2" - 8"
Flanges 1/2" - 8"
Bar 1" - 6"
SPECIFICATIONS
ASTM B407, B514, B366, B408, B564
ASME SB407, SB514, SB366, SB408, SB564
DESCRIPTION
Alloy 800 is a widely used material of construction for equipment that must resist corrosion, have high strength or resist oxidation, carburization and other harmful effects of high-temperature exposure. For high temperature applications requiring optimum creep and rupture properties Alloy 800HP is used. The Chromium in the alloy imparts resistance to oxidation and corrosion. The high nickel content maintains an austenitic structure so that the alloy is ductile. The nickel also contributes resistance to scaling, general corrosion and stress corrosion cracking. The iron content provides resistance to internal oxidation.
DESIGN FEATURES
Good creep-rupture properties at temperatures above 600 deg. C (1110 deg.F) without loss of ductility during long term use at temperatures below 700 deg. C (1290 deg.F), due to limitation of (Ti & A) content to max 0.7%. However, by using 800HP with increased (Al & Ti) content to 1.2%, temperatures above 700 deg. C (1290 deg.F) can be achieved.
Good resistance to reducing oxidizing and nitriding atmospheres and to atmospheres which alternates between reducing and oxidizing conditions.
Metallurgical stability in long-term applications at high temperatures.
TYPICAL APPLICATIONS
Steam / hydrocarbon reforming for components such as pig tails, headers, collectors, manifolds, transfer piping, catalyst tubes, and quench system piping
Ethylene pyrolsis tubing in convection and radiant sections - resistance to carburization and good mechanical properties
Ethylene dichloride cracking tubes - resistance to carburization and to dry hydrogen chloride and chlorine
Components, eg. Heat exchangers, piping systems, etc... in coal conversion plants
Steam generators tubing in helium coolant, high temperature reactor systems - high strength, resistance to helium and steam
TENSILE REQUIREMENTS
Tensile Stength (KSI) 72.5
Yield Strength (KSI) 25
KSI can be converted to MPA (Megapascals) by multiplying by 6.895.
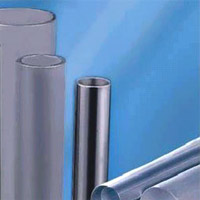
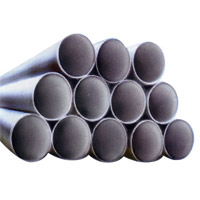
AVAILABILITY
Seamless Pipe 1/2" - 8"
Welded Pipe 8" - 12"
Butt-Weld Fittings 1/2" - 8"
Flanges 1/2" - 8"
Bar 1" - 6"SPECIFICATIONS
ASTM B443, 8705, 8366, B425, B564
ASME SB443, SB705, SB366, SB925, SB564
DESCRIPTION
Alloy 825 is a nickel-iron-chromium alloy with additions of molybdenum, copper and titanium. The alloys chemical composition provides exceptional resistance to many corrosive environments. The nickel content is sufficient for resistance to Chloride-ion stress corrosion cracking. The nickel, combined with molybdenum and copper, also gives outstanding resistance to reducing environments such as those containing sulfuric and phosphoric acid. The molybdenum also aids resistance to pitting and crevice corrosion. The alloys Chromium content confers resistance to a variety of oxidizing substances such as nitric acid, nitrates and oxidizing salts. The titanium addition, with appropriate heat treatment, will stabilize the alloy against sensitization to intergranular corrosion.
DESIGN FEATURES
Good resistance to stress corrosion cracking.
Satisfactory resistance to pitting and crevice corrosion.
Good resistance to oxidizing and non-oxidizing hot acids.
Good mechanical properties at both room and elevated temperatures up to approximately 550 deg.C (1020 deg. F).
Permission for pressure-vessel use at wall temperature up to 425 deg. C (800 deg. F).
TYPICAL APPLICATIONS
Components such as heating coils, tanks, crates, baskets and chains in sulfuric acid pickling plants
Fuel element dissolvers-the alloy withstands the different media (sulfuric and nitric acids, caustic hydroxide etc.) used in processing
Sea water cooled heat exchangers; offshore product piping systems tubes and components in sour gas service - resistant to chloride-ion stresscorrosion cracking
Pipelines carrying wet sulphur dioxide gas and pulp digesters in the papermaking process
Heat exchangers, evaporators, scrubbers, etc. used in phosphoric acid production
Air cooled heat exchangers used in the processing of liquid petroleum gas (LPG)
TENSILE REQUIREMENTS
Tensile Strength (KSI) 85
Yield Strength (KSI) 35
KSI can be converted to MPA (Megapascals) by multiplying by 6.895.
- Pipes & Tubes
- Steel Elbows
- Steel Tees
- Steel Reducers
- Steel Caps
- Steel Stub-Ends
- Flanges
- Fasteners
- High-Performance Alloys
- Sheets, Plates & Coils
- High Nickel & Chromium Alloys
- Alloy 20
- Avesta Sheffield 2205
- Alloy C-276
- Stainless Steel 310S
- Stainless Steel 321/321H
- Stainless Steel 347/347H
- Alloy AL-6XN
- 254SMO
- Alloy 6061 T6
- Stainless Steel 317L
- Alloy 904L
- Alloy 410 / 410S
- Stainless Steel 304/304L
- Stainless Steel 316/316L
- Alloy 200
- Alloy 400
- Alloy 600
- Alloy 625
- Alloy 800 / 800H / 800HP
- Alloy 825